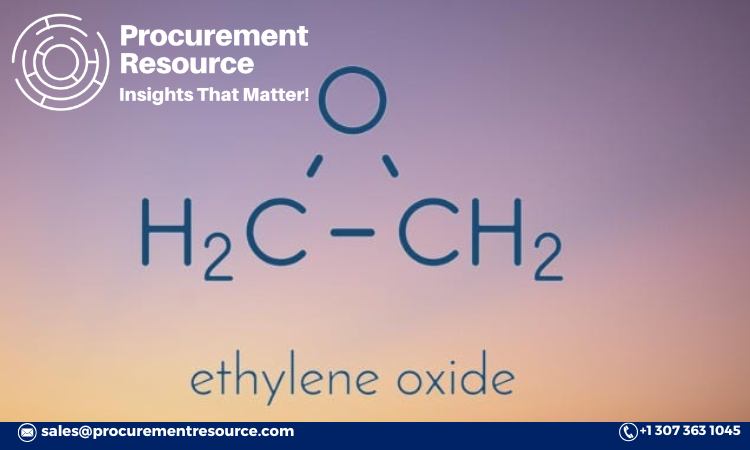
Ethylene oxide (EO) plays a pivotal role in the manufacturing of numerous industrial and consumer products, including antifreeze, textiles, plastics, and personal care products. Given its extensive use, it is crucial for businesses operating in these sectors to understand the ethylene oxide production cost. Gaining insight into the cost components, trends, and market dynamics surrounding ethylene oxide production can help companies optimize their procurement strategies, enhance production efficiency, and maintain competitive pricing.
This article provides a detailed overview of the ethylene oxide production process, associated costs, and the factors influencing its market. For businesses looking to streamline operations or reduce costs, this analysis will serve as an essential resource.
Request a Free Sample For Ethylene Oxide Production Cost Reports
Ethylene Oxide Production Process: Overview
Ethylene oxide is primarily produced using the catalytic oxidation of ethylene in the presence of oxygen. The process typically takes place in a fixed-bed reactor using a silver-based catalyst under high temperature (200-300°C) and pressure (10-20 bar). This process involves several stages:
Feedstock Preparation: Ethylene, derived from hydrocarbon cracking or natural gas, is purified and prepared for the reaction.
Catalytic Oxidation: Ethylene and oxygen (or air) are introduced into a reactor containing a silver-based catalyst. The reaction forms ethylene oxide along with water as a by-product.
Separation and Purification: Ethylene oxide is separated from water, unreacted ethylene, and other impurities using techniques like gas absorption, condensation, and distillation. The final product undergoes purification to meet specific quality standards.
This process is energy-intensive, and its costs are influenced by several factors, including raw materials, energy consumption, and catalyst efficiency. Optimizing these variables is key to minimizing production costs and improving the overall profitability of the ethylene oxide manufacturing process.
Read Full Report: https://www.procurementresource.com/production-cost-report-store/ethylene-oxide
Procurement Resource Assessment: Ethylene Oxide Production Cost
At Procurement Resource, we break down the various factors contributing to ethylene oxide production costs. Our reports focus on the following aspects to provide a comprehensive view of cost drivers:
Raw Material Costs: Ethylene is the primary feedstock for ethylene oxide production, making up a significant portion of the total cost. The price of ethylene is heavily influenced by global oil and gas markets, making it a key determinant in the cost structure of ethylene oxide production. Additionally, oxygen or air used in the catalytic process is another crucial raw material, with associated procurement and handling costs.
Energy Consumption: The ethylene oxide production process requires large amounts of energy to maintain the necessary high temperatures and pressures in the reactors. This energy demand translates into substantial electricity or natural gas costs, depending on the energy source used by the facility.
Catalyst Costs: The silver-based catalyst used in the oxidation process is another important component of the cost structure. Although catalysts have a long lifespan, they need to be replaced periodically, and high-quality catalysts come with a premium price.
Capital Investment and Equipment Maintenance: Setting up an ethylene oxide production facility involves significant capital investment in reactors, separators, and other necessary equipment. Maintenance and upkeep are ongoing expenses that must be factored into the production cost.
Environmental Compliance: Given that ethylene oxide is a hazardous substance, regulatory compliance is essential. Investing in emissions control technologies and adhering to environmental standards are necessary for businesses to avoid penalties, adding to overall production costs.
Ask an Analyst: https://www.procurementresource.com/production-cost-report-store/ethylene-oxide/ask-an-analyst
Trypsin: A Complementary Element in Sterilization
In industries where ethylene oxide is used as a sterilizing agent—such as pharmaceuticals and medical devices—trypsin can be used as a complementary treatment. This proteolytic enzyme helps degrade proteins on surfaces, allowing for more effective sterilization when combined with ethylene oxide. Understanding the use of trypsin in combination with EO sterilization is important for businesses operating in healthcare or related industries.
Market Drivers Influencing Ethylene Oxide Production Cost
Several market drivers have a direct impact on the cost of producing ethylene oxide:
Increasing Demand in Medical Applications: Ethylene oxide is widely used for sterilizing medical equipment and pharmaceuticals. With the growing healthcare sector driven by aging populations and increased healthcare spending, the demand for ethylene oxide is rising. This increased demand can lead to upward pressure on production costs.
Growth in Polyester Manufacturing: Ethylene oxide is a key component in the production of ethylene glycol, which is used to manufacture polyester fibers. The expanding textile and packaging industries, especially in regions like Asia-Pacific, are driving up demand for ethylene oxide.
Green Energy Transition: Ethylene oxide is also used in producing bio-based chemicals and fuels. As the global focus shifts toward cleaner energy sources, ethylene oxide’s role in producing sustainable materials will continue to grow, impacting its production and associated costs.
Technological Advances: Advances in production technology can significantly influence production costs. By improving catalyst efficiency and optimizing energy usage, manufacturers can reduce operating expenses. However, these innovations may require capital investments, which could increase short-term costs.
Raw Material Requirements
The main raw materials for ethylene oxide production include:
Ethylene: As the key raw material, ethylene is sourced primarily from hydrocarbon cracking or natural gas. Its availability and cost depend heavily on global market conditions, particularly in the oil and gas sectors.
Oxygen (or Air): Oxygen is required for the oxidation process, and its procurement and handling must be factored into the production cost.
Catalyst: Silver-based catalysts play an essential role in facilitating the reaction, and while they are long-lasting, their periodic replacement contributes to production costs.
Understanding the specific requirements for raw materials and their associated costs is critical for optimizing ethylene oxide production.
Costs and Key Process Information
The total cost of ethylene oxide production is influenced by several key factors:
Capital Investment: Building a production facility involves substantial upfront capital, with costs for reactors, purification systems, and safety equipment.
Operating Costs: Energy consumption, labor, and maintenance costs are ongoing operating expenses that businesses must account for.
Regulatory Costs: Compliance with environmental and safety regulations is essential in ethylene oxide production, requiring investments in emissions control technologies and monitoring systems.
Looking for an Exhaustive and Personalized Report?
For businesses looking for detailed insights into the ethylene oxide production process, our customized reports offer a thorough breakdown of production costs, procurement strategies, and market trends. A personalized report can help you optimize your production processes, stay competitive, and navigate the complexities of the global ethylene oxide market.
Our reports provide a granular analysis of every cost component, from raw materials to environmental compliance, giving you a comprehensive understanding of how to manage and reduce expenses. Whether you’re a manufacturer, procurement officer, or investor, our tailored reports will provide actionable insights to help you make informed decisions.
Request a Free Sample - https://www.procurementresource.com/production-cost-report-store/ethylene-oxide/request-sample
Contact Us:
Company Name: Procurement Resource
Contact Person: Endru Smith
Email: sales@procurementresource.com
Toll-Free Numbers:
USA & Canada: +1 307 363 1045
UK: +44 7537171117
Asia-Pacific (APAC): +91 1203185500
Address: 30 North Gould Street, Sheridan, WY 82801, USA
Write a comment ...